Crafting the Future with Passion and Precision at Cherry
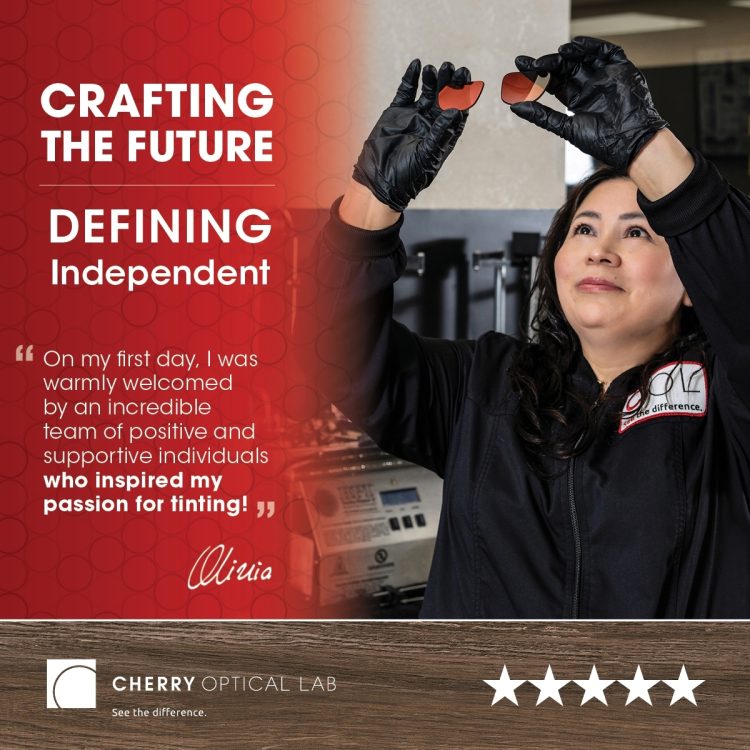
Crafting the Future – Defining Independent
For decades, the basic definition of an Independent optical Lab was a Lab that is not owned (majority or minority stake) by a lens manufacturer. Updating that definition for today’s times should probably include laboratories that are not controlled by venture capital groups. Finally, perhaps a capital “I” for Independent should be reserved for Labs that are similarly not controlled, aligned, or supportive towards discount vision plan providers. Regardless of your definition of independence, there is no debate about the fact that the meaning has evolved.
We genuinely believe that having robust Independent Optical Lab partners is integral to the success of private eye care. At Cherry, like most Labs, we focus on four pillars: high-quality finished products, fast turnaround times, expert support, and innovation. All Labs should know these are important to their customers, and if you searched a few websites, they’d likely say most of those same things. So, what makes us different?
To set expectations and show you the “Cherry difference,” we’re excited to share our aspirations. We’re crafting our future by expanding our capabilities and highlighting the advancements and the people who help us define what makes us a robust Independent Lab choice. We intend to use our advertisements as outlets to provide more transparency about the “why and how” we do what we do at Cherry. To show you how we dig deeper than your “other Lab,” we will focus on our Tint Operations to kick things off.
Our Mindset Surrounding Tint is like No Other
It is commonplace at most optical laboratories, and it happened at COL multiple times, that Tint takes the backburner [pun intended]. It was crucial for us to recognize Tint as an indispensable component of our operations. Tint has often been overlooked industry-wide, particularly as it is typically associated with Finish Operations and may be considered a stepping stone for the career growth of Finish Laboratory Opticians. We knew we needed to change our perspective and acknowledge Tint for the value it truly brings – in terms of revenue it generates, expertise it takes to do it correctly, and financial benefits to those dedicated to the craft. Our Leadership Team engaged in discussions that questioned the existing industry norms, acknowledged our previous missteps, and established clear expectations for what eventually evolved into our Tint Center of Excellence. We needed to develop a mindset where Tint as a department stands on its merit; our Happy Humans helped us get there.
Our Happy Tint Team
We must have the right individuals in place to successfully achieve our goal of Excellence. As "tinting" is no ordinary job, we seek out individuals who relish the challenge and artistic nature of tinting. Equally important, we search for individuals willing to collaborate and share their expertise and knowledge. The pursuit of improvement is an ongoing journey, and our Team Members must be aligned with this mindset and genuinely desire to facilitate each other's success. We have, by far, the best team we’ve ever had in our Tint Center right now, and we will only add new people who maintain or improve the culture we worked so hard to develop.
As part of ensuring the Tint department stands on its merit, we set clear expectations for the quality of work produced, quantity produced, and general ability to be a genuinely Happy Human Tint Team Member. We knew that if we wanted to challenge that status quo and truly live up to the title of Tint Center of Excellence, we had to be willing to compensate our Team Members within the department. So, we developed a process that allows Tint Team Members to demonstrate advanced abilities to earn the title of a Tint Master. Considering our elevated expectations for these Team Members and the revenue generated from tint operations, it was easy to justify raising the wages - increasing the starting wage for future Team Members and providing even further wage increases for those who become masters of their craft. One of our Tint Masters is featured in this ad.
Meet Olivia Aguayo – Tint Master
Where we were, where we are, and where we are going with tinting is all about ensuring our Team has the tools and resources needed to exceed customer expectations consistently. Olivia (pictured in the ad) has done an incredible job and adapted exceptionally well to our major initiative to elevate all things tinting. Olivia joined the Cherry family in 2020. In addition to her dedication to our team, we’re also impressed with her dedication to bettering herself; in 2022, Olivia achieved an inspiring accomplishment. She passed her citizenship test. Did you know there are 100 questions on the official USCIS naturalization test? On test day, an immigration officer verbally asks 10 out of the 100 previously mentioned questions. You must answer at least six correctly to pass the test, and it’s not easy. We are so proud of her and her achievements both internally and outside of the Lab. Since becoming a Tint Master, she has led our team ferociously.
In addition to Olivia, we have another Team Member whose natural talent for tinting earned her promotion to Tint Master - Maddie Basken. Maddie began with Cherry in 2021 and has an eye for production and training. Her skill level alone could help her achieve this title, but she has many great qualities that sealed the deal. These two Happy Tinters emulate the Happy Human culture; we’re grateful to have them leading our team of skilled artisans. They’ve truly helped us to take tinting to the next level.
Here are a few words from Olivia, "On my first day, I was warmly welcomed by an incredible team of positive and supportive individuals who inspired my passion for tinting. With their invaluable guidance, I have transitioned from student to teacher, proudly earning the title “Tint Master.” This opportunity allows me to share my knowledge and uplift my peers, and I couldn’t be more thrilled!"
You Can Have the Right People, but they Need the Right Tools
We have extensively researched to find the most stable and capable tinting equipment available. Instead of mass-producing thousands of frames in one color and material, we take a unique approach at Cherry Optical Lab. Almost every tint job involves a distinctive shape, color, material, and coating combination. We don’t shy away from challenging tasks either. That's why we have settled on a battalion of Turbo 2 Tinters from BPI. These tinters maintain a stable temperature throughout the entire beaker, conserving tint and water by preventing overheating or boiling over.
To better the machines further, our Continuous Improvement team member, Brian Gerondale, worked with a local manufacturer to fabricate custom drip trays. By observing the process and evaluating the machinery, we were able to implement changes that reduce the possibility of getting Tint anywhere near the job trays and prevent anyone/anything from accidentally shutting down the machine during operation. In addition to the drip trays that protect the display screens, angled hoods were added to the back of the machines to deflect Tints and hot liquids from shorting out the temperature probes, reducing damage to the machine itself and to lenses that could have overheated. We also use large hot water heaters to properly warm water to quickly swap out or refresh the different dyes, reducing the wasted time waiting for the tint to warm. Speaking of water, we also invested in a water distillation and filtration system to ensure the water used in our tinting process is as pure and free of contaminants as possible. For consistency, we utilize BPI’s gradient dippers, BPI’s spectrometer for measuring color, and Multimeters from OptiSource for varying UV performance and tint density. It’s been a journey, but when the goal is “Excellence,” the drive to constantly seek better is easy to maintain.
How Did We Figure This All Out?
Constantly Learning – We must constantly learn to maintain and further improve our tinting operations. We cannot claim to be “Seekers of Better” or “Process Pioneers” without committing to our education and sharing our findings. We must document our process and share insight across departments and shifts to maintain consistent, high-quality results. New materials, coatings, and process changes directly impact tint results. Examples include changing the spin coating lacquer, changing the lacquer's curing time, increasing the UV lamp's intensity, or changing the time it takes to get from coating to tinting. That’s just one example! Does one MFR’s polarized lens take HC better than another? How about Transitions? Even little things like the type of tape used in surfacing or what type of AR will be applied to the tinted lens can impact what our Tint Team Members need to be mindful of. Interestingly, a big part of our current learning process is defining which combinations will tint well, which are more difficult, and which are nearly impossible to complete without a significantly higher risk of scrap. Our goal is to be able to share with our customers the best design and material combinations to ensure their tint jobs are done perfectly and quickly.
Defining Independent
By ensuring we never lose sight of the four pillars we know our customers value: high-quality finished products, fast turnaround times, expert support, and innovation - and focusing on what improvements we know will elevate our Customers’ Experiences, we are defining our Independence. Our Laboratory has the autonomy to adapt and react, when necessary, without all the overhead. It’s one of the best parts of being a family-owned Independent Optical Laboratory, and we hope you truly do “See the Difference.”
Categories