And Then There Were Three - We Are Leaping With Excitement!
The contents of this box are being installed this week. Can you guess what it is?
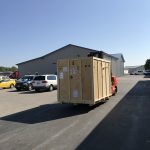

We are currently running two additional models of this Schneider Optical machine. It arrived from Germany and should fully up and running by mid-week. Check out the new video below highlighting the machines in the new arrival's destined area of production and get ready for even quicker turn-around times!
Digital Surface - Part 1 - The “Front End” of Digital Surfacing. This video will show the first few steps used in the digital and freeform surfacing of optical lenses
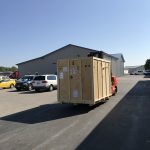

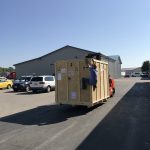
- After removing the semi-finished lenses from their packaging, the lenses are queued to be processed by the automated lens taper.
- The taper applies a mildly adhesive 1-sided tape to the lens. This tape protects the front surface of the lens from heat and physical damage as the lens goes through the digital surfacing steps.
- Taped lenses are ready to be blocked utilizing our SCHNEIDER and Optotech alloy blockers.
- Surface blockers apply a block piece (chuck/handle) to the lens at the proper alignment and angle needed to ensure axis and prism alignment.
- Lenses are blocked by selecting the correct block piece and blocking ring (based on the front curvature and final diameter of the lens being produced).
- The lens is then positioned correctly before being lightly clamped into position.
- A special metal alloy that melts at a very low temperature and can repeatedly be melted and rehardened is introduced to fill the cavity between the front surface of the lens and the block piece created by the blocking ring.
- The metal hardens to a point that it can be removed from the surface blocking machine within 20 seconds.
- Blocked lenses then “chill” for 40 minutes to ensure all heat has dissipated and metal alloy has fully hardened.
- Blocked lenses are now ready to go through the digital and freeform surfacing generators - better described as lathes.
- The SCHNEIDER generators gather and calculate the proper processing information by scanning the barcode on the tray and communicating with the LMS (lab management software).
- Freeform lens orders receive a custom-calculated height-map file (topography) that was created by the lens designers property software. This height-map is the freeform design.
- Automation of loading into the generator ensures maximum machine efficiency and processing time.
- The first step is to mill the lens to its final diameter and within 0.5 mm of its final thicknesses. An aggressive 12-bit milling tool, spinning at 35,000 rpm achieves this result in 10-15 seconds.
- The lens then moves down to an extremely precise lathing processes that utilizes SCHNEIDER's patented RS-TEC motor to control the cutting path of a natural diamond tipped tool.
- As the lens spins at 300 to 3500 rpms, the diamond tipped tool is moving from outside-to-inside of the lens, moving in-and-out to create the complex topography illustrated by the lens design file
- Every 1-2 minutes, a digital or freeform lens is completed and returned to the job tray.
Categories